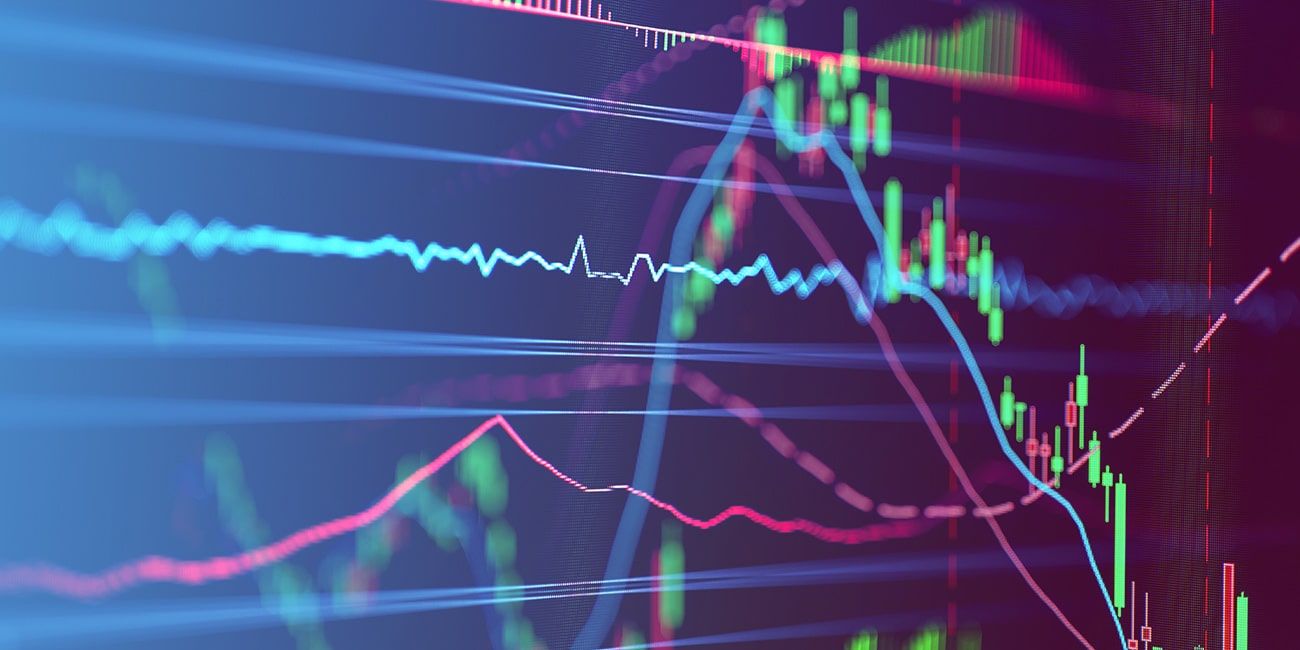
Today’s customers want to return items quickly, easily and for free. These demands put a strain on logistics teams at e-commerce companies of all sizes.
To create a positive return experience for the customer in a way that is effective and efficient for the company, businesses need to tackle the challenges that come with processing returns.
USPS® recently commissioned Provoke Insights to conduct a proprietary study into the e-commerce reverse logistics landscape.
32% of surveyed companies cited manual labor tasks, including reworking, repacking and relabeling, as the biggest challenge to returns.[1]
After identifying what isn’t working in the returns process, turn to technology. Implementing the right hardware and software can relieve time-consuming manual tasks that slow down the productivity and efficiency of fulfillment employees. More than two-thirds (67%) of companies are already improving their logistics processes with technology.[2]
Research indicates that these four technologies provide opportunities to enhance and optimize your returns process.
Automatic Data Capture 1
Identify a returned object and gather important data about it without ever opening a package by using scannable barcodes or RFID tags.
44% of surveyed companies use automatic data capture.[3]
Primarily, automatic data capture cuts down the amount of valuable employee time spent opening a package, identifying an item, logging the reason for return and deciding where that package goes next.
When a customer initiates a return online, they can note why they are returning the item. Then, a specific barcode is generated for their return label. Back in the warehouse, a team member can simply scan that code to see if the item is damaged and ineligible for resale or if it was simply the wrong fit for the customer.
Cloud Computing 2
Log and store valuable information about each return—such as the type of return, status, and more—in an accessible shared space.
37% of surveyed companies use cloud computing.[4]
The cloud is, in short, internet storage. Rather than managing reports and data on a local computer or server, which requires timely back-and-forth between a network of internal and external stakeholders, businesses can use the cloud for faster and more efficient visibility.
Most cloud-based management applications also incorporate some level of live editing, meaning stakeholders can see logged updates in near-real time. It also opens the door to better collaboration with partners and broader visibility across the supply chain.
Predictive Analytics and Big Data 3
Discover insightful patterns through data analysis that can forecast and help get ahead of future returns.
25% of surveyed companies use predictive analytics with big data.[5]
Using all the data collected from the returns process—including the reasons for returns, as well as their frequency and volume—predictive analytics technology can identify and flag issues that might otherwise have gone undetected.
For example, if there is a large volume of returns on one item that arrived damaged, the instance would be flagged. Then, a fulfillment team could pre-empt future returns by changing the packaging for that item to prevent issues going forward.
Predictive analytics informed by big data are time- and money-savers for logistics teams.
Blockchain 4
Track and verify returns against the original transactions to scale back the time and labor of manually checking returns against receipts.
14% of surveyed companies use blockchain.[6]
While blockchain technology is still in the early stages of development and use, it is quickly gaining traction and offers a lot of value. The digital ledger of blockchain, which allows information to be digitally distributed but not manipulated or copied, creates a transparent record of a shipment. With this true record, it’s easy to see whether what is in the package when returned matches what was in the package when originally shipped.
Implementing digital ledger technology scales back the manual labor needed for fulfillment employees to verify returns, allowing them to return focus to their primary roles.
Which of the technologies covered above would be most helpful to your team?
Key Takeaway
These four technologies have been embraced by a number of companies as the keys to an optimal returns process. Leverage one or all of these options and see how technology can help streamline reverse logistics for your business.
While technology offers value for a modern e-commerce business dealing with returns, the landscape of reverse logistics is vast. Discover actionable insights from top companies to tackle seamless product returns head-on: Our full report is an insider guide, rich with proprietary research from Provoke Insights, that can help any business create a sustainable and competitive returns process.
Footnotes
keyboard_arrow_down- [1]“Reverse Logistics in Today’s Digital Landscape,” Proprietary survey of 300 e‑commerce professionals conducted by Provoke Insights, Aug. 2019. arrow_right_alt
- [2]Ibid. arrow_right_alt
- [3]Ibid. arrow_right_alt
- [4]Ibid. arrow_right_alt
- [5]Ibid. arrow_right_alt
- [6]Ibid. arrow_right_alt